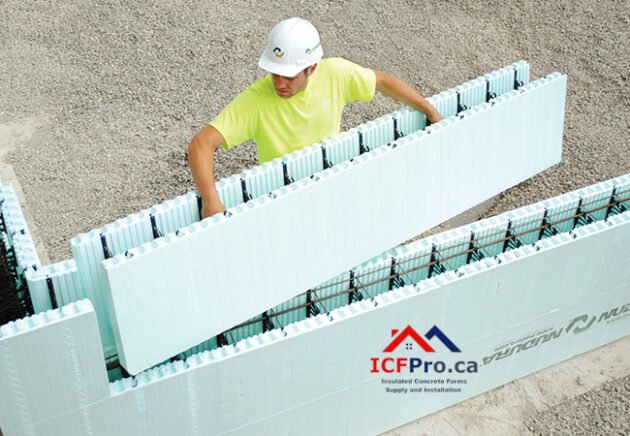
🏗️ ICF vs. SIPs: A Comprehensive Comparison of Modern Building Systems
The construction industry is evolving rapidly, driven by the need for energy efficiency, resilience, and faster building methods. Among the leading innovations are Insulated Concrete Forms (ICF) and Structural Insulated Panels (SIPs), both designed to enhance thermal performance, reduce construction timelines, and promote sustainable building practices.
Choosing between ICF and SIPs depends on various factors, including climate, budget, and project type. This article explores their differences, advantages, and ideal applications, helping builders, architects, and homeowners make informed decisions.
1. What Are ICF and SIPs?
🧱 ICF (Insulated Concrete Forms)
ICF involves stacking interlocking foam blocks—usually made from expanded polystyrene (EPS)—to form wall structures. These hollow blocks are filled with reinforced concrete, while the foam remains in place as permanent insulation. The result is a solid, monolithic wall system known for its high thermal mass, strength, and durability.
🏠 SIPs (Structural Insulated Panels)
SIPs consist of a rigid foam core (EPS, XPS, or polyurethane) sandwiched between two structural facings, typically oriented strand board (OSB). These panels are factory-manufactured to precise specifications and assembled on-site, ensuring rapid construction and airtight building envelopes.
2. 🔍 Key Differences at a Glance
Aspect | ICF | SIPs |
---|---|---|
Material Composition | Foam blocks filled with reinforced concrete | Foam core with OSB/plywood facings |
Insulation | High thermal mass stabilizes indoor temperatures | Continuous foam core reduces thermal bridging |
Strength | Extremely durable; resists fire, wind (200+ mph), and pests | Structurally sound but vulnerable to moisture damage |
Cost | Higher upfront costs but long-term energy savings | Lower initial costs and reduced labor expenses |
Construction Time | Longer due to concrete curing and labor-intensive work | Faster assembly with prefabrication |
Design Flexibility | Limited by wall thickness but adaptable to curved walls | Customizable but requires precise planning |
3. ✅ Pros and Cons of ICF
🟢 Advantages of ICF
- Superior Durability: ICF walls are exceptionally strong, and capable of withstanding hurricanes, earthquakes, and tornadoes. The reinforced concrete core resists fire, pests, and mold.
- Energy Efficiency: ICF’s thermal mass stabilizes indoor temperatures, reducing heating and cooling demands by 20–40% compared to traditional construction.
- Soundproofing: ICF offers excellent acoustic insulation, with Sound Transmission Class (STC) ratings of 45 to 50+, effectively blocking external noise.
- Disaster Resilience: Concrete cores make ICF homes highly resilient against natural disasters, including wildfires and floods.
🔴 Drawbacks of ICF
- Higher Costs: ICF can cost 5–10% more than SIPs, primarily due to concrete and labor expenses.
- Thicker Walls: ICF walls are typically 12–16 inches thick, reducing interior square footage and complicating retrofits.
- Environmental Impact: Concrete production contributes significantly to CO₂ emissions, although ICF’s energy efficiency offsets this over time.
4. 🟩 Pros and Cons of SIPs
🌟 Advantages of SIPs
- Speed and Affordability: SIPs arrive prefabricated, reducing construction timelines by 30–50% and cutting labor costs.
- Energy Efficiency: SIPs achieve impressive R-values up to R-50, outperforming conventional framing and enhancing airtightness.
- Eco-Friendly: SIPs use renewable OSB facings and generate less on-site waste compared to traditional framing.
⚠️ Drawbacks of SIPs
- Moisture Sensitivity: OSB facings are vulnerable to mold, rot, and structural degradation if exposed to moisture.
- Lower Thermal Mass: SIPs lack the heat-storing capacity of ICF, making them less effective in extreme climate zones.
- Design Rigidity: SIPs require precise prefabrication, making post-fabrication changes complex and costly.
5. 💰 Cost Comparison: Upfront vs. Long-Term Savings
Cost Category | ICF (Approx.) | SIPs (Approx.) |
---|---|---|
Material Cost (per sq. ft.) | $7 – $10 | $6 – $15 |
Labor Cost (per sq. ft.) | $14 – $20 | $8 – $12 |
Total Installed Cost | $35 – $45 | $19 – $35 |
Energy Savings (Annually) | 20% – 40% | 30% – 50% |
Long-Term Maintenance | Low, durable concrete structure | Moderate, requires moisture control |
While ICFs may cost more initially, they offer long-term energy savings and minimal maintenance. SIPs, on the other hand, provide a more affordable upfront solution but require diligent moisture management.
6. 🌎 Which Is Better? It Depends on Your Project
❄️ Climate Considerations
- ICF: Ideal for extreme climates, including areas with temperature fluctuations, wildfires, hurricanes, or heavy snowfall.
- SIPs: Best for temperate climates where rapid heating and cooling efficiency are priorities.
🏗️ Project Type
- ICF: Preferred for multi-story buildings, basements, and disaster-prone areas requiring robust structural integrity.
- SIPs: Optimal for residential homes, light commercial structures, and projects requiring fast, cost-effective construction.
🔄 Hybrid Approach
Combining ICF walls with SIP roofs can leverage the best of both systems—ICF’s strength and thermal mass alongside SIP’s insulation and speed.
7. 🌿 Environmental Impact: Which Is More Sustainable?
Environmental Factor | ICF | SIPs |
---|---|---|
Carbon Footprint | Higher due to concrete production | Lower, especially when using sustainable OSB |
Energy Efficiency | High, with reduced HVAC reliance | Higher R-values but lower thermal mass |
Material Waste | Minimal due to on-site assembly | Low, with prefabrication reducing waste |
Recyclability | Foam and concrete are difficult to recycle | OSB and foam can be recycled or repurposed |
While SIPs have a lower embodied carbon footprint, ICFs often compensate through superior long-term energy efficiency.
8. 🌪️ Resilience in Natural Disasters
- Hurricanes and Tornadoes: ICF walls can withstand winds over 200 mph, making them superior for storm-prone areas.
- Earthquakes: ICF’s reinforced concrete core offers excellent seismic resilience.
- Fire Resistance: ICF provides up to a 4-hour fire rating, while SIPs typically offer 1–2 hours depending on the facing material.
- Flooding: ICF resists water intrusion, while SIPs risk structural damage if submerged.
9. 🕰️ Long-Term Performance and Maintenance
Performance Factor | ICF | SIPs |
---|---|---|
Lifespan | 100+ years with minimal maintenance | 50–70 years, contingent on moisture control |
Pest Resistance | Excellent, impervious to termites | Vulnerable, especially if OSB is exposed |
Maintenance Needs | Low; occasional inspection | Moderate; moisture and sealing checks |
10. 🎯 Conclusion: Which System Should You Choose?
The ICF vs. SIPs debate doesn’t yield a universal winner—it ultimately depends on project-specific needs, budget, and environmental conditions.
- Choose ICF if you prioritize:
- 🛡️ Structural resilience against disasters
- ❄️ Long-term energy efficiency and low maintenance
- 🔇 Superior soundproofing and durability
- Choose SIPs if you prioritize:
- 🚀 Faster, cost-effective construction
- 🌡️ High insulation values and airtightness
- 🌳 Eco-friendly materials with reduced carbon footprint
For those seeking the best of both worlds, a hybrid system—ICF walls with SIP roofs—offers an optimal balance of strength, efficiency, and affordability. You can also check the article on our sister site ICFpro.ca.